Novel digital holographic and modelling technologies for unlocking the metal-ceramic co-deposition mechanism during supersonic cold spray
Project Coordinator
Dr. Shuo Yin
yins@tcd.ie
+353 189 5358
Leo Devlin
devlinle@tcd.ie
Yasin Amani
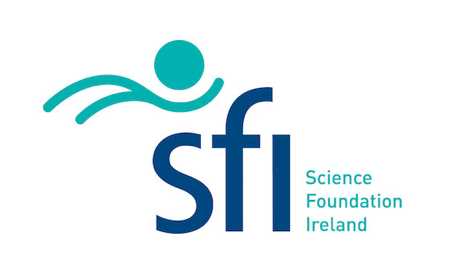
Description
High-velocity impact is an important physical phenomenon that can be seen in many fields and in various scales, from catastrophic impact of asteroids on planets, to macro-scale impact of bullets on armours, and to micro-scale impact of airborne or space dust particles on object surfaces. Some of these impacts are harmful and have to be avoided, while the others are beneficial and can be used by us. As an emerging material deposition technology, supersonic cold spray (CS) is a beneficiary of “good” impacts. When metal microparticles impact onto a metal substrate at “subsonic” or “supersonic” speed (ranging from 300 m/s to 1000 m/s), they will undergo severe plastic deformation with ultra-high strain rate (up to 109/s at localized region), and stick on the substrate to form a thick coating without crossing the melting temperature. On the basis of this fact, CS was thus developed. As the only available solid-state metal deposition technique, CS adds significant advantages to fusion-based thermal spray processes, such as high deposition efficiency, high thickness, low thermal effect on the substrate and free of phase transformation. Today, the rapid development of manufacturing industry has come to push the boundary of CS application window from surface modification to additive manufacturing (AM). As compared with conventional fusion-based AM technologies, CS demonstrates superiority due to its short production time, unlimited product size, high flexibility and suitability for damaged component repair. Particularly, its non-fusion advantage enables CS a perfect process for manufacturing certain ceramic-reinforced metal matrix composites (MMCs), such as Al-SiC for thermal management and Cu-W for nuclear industry.
Since the invention of CS, particle-substrate and particle-particle bonding mechanisms have been a primary research topic. It has been revealed that, for CS pure metal deposits, the bonding is dominated by nanoscale metallurgical reaction originate from localized high-strain-rate plastic deformation (up to 109 s-1 at the metal-to-metal interfaces. However, for CS MMC deposits, due to the introduction of additional ceramic particles, the particle deposition process becomes more complicated. To date, the substantial metal-ceramic co-deposition mechanism (e.g., mutual interactions between metal and ceramic particles) during the fabrication of MMC deposits is still not understood. It is clear that the lack of such critical knowledge is a hard barrier for the further evolution of CS technology and significantly prevents the development of high-performance CS MMC deposits. Currently, the most prevailing hypothesis for the co-deposition mechanism is that the cohesion of metal particles follows the aforementioned metal-to-metal bond mechanism while ceramic particles deposit through penetration and interlocking into the metal phase. This hypothesis has never been proved so far because the established experimental technologies are incapable to capture the three-dimensional (3D) real-time co-deposition process that completes within nanoseconds. Even a reliable numerical model that can precisely simulate the co-deposition process is still not available. Therefore, many critical issues with regard to the co-deposition have not been addressed and clarified. For example, ⅰ) why ceramic particles fail the deposition in single impact but deposit during the formation of full-scale coating, ⅱ) why some ceramic particles fracture in the coating but the others not, ⅲ) how the supersonic gas flow and in-coming particles influence rebound particles, ⅳ) how ceramic and metal particles interact with each other. For a technological breakthrough in CS to be feasible, a thorough understanding of the fundamental co-deposition mechanism is imperative. The “key” for this is a high spatial and temporal resolution imaging analysis along with a new modeling framework. It is plausible that a thorough understanding of the mechanism behind the metal-ceramic co-deposition will guide feedstock powder preparation, deposition parameter optimization and new CS system development, making CS more efficient and economical for the fabrication of high-performance (e.g., high mechanical proeprties, high thermal conductivity, high electrical conductivity, high wear resistance) MMC deposits with tailored microstructure.