The Technical and Commercial Development of Cold Spray Applications in Ireland
Project Coordinator
Dr. Rocco Lupoi
Email: [javascript protected email address]
Tel: +353 1 896 1729
Dr. Shuo Yin
Email: [javascript protected email address]

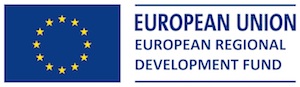
Description
This project aims to develop the cold spray technique in Ireland for various industrial applications. We have currently been working on several materials so far. Among these works, the most promising ones can be regarded as the WC-Co coating for wear-resistance and copper-diamond coatings.
WC-17Co/WC-17Co+Ni onto Stainless steel substrate for wear-resistance
The cold sprayed WC-17Co coating onto stainless has been fabricated. Fig. 1a shows the cross-sectional SEM image of the WC-17Co coating. The coating is dense with very small porosity. But the deposition efficiency for this coating is not quite high which means a relatively large demand of powders and gas is needed.
To deal with this problem, we attempted to use pre-mix WC-17Co and Ni (Ni is also a very promising material for wear-resistance) as the feedstock. Ni can act as a binder to facilitate the coating formation. We added 20 wt. % of Nickle into WC-17Co powders and pre-mixed them before spraying. Fig. 1b show the cross-sectional images of the Ni+WC-17Co coating.
The results indicate that using the mixed powder of WC-17Co and Ni as the feedstock significantly increases the deposition efficiency. The deposition efficiency reaches more than 80%. At the same time, the fraction of WC-17Co inside the coating is also satisfactory, reaching about 55 wt.%.
Fig. 1. Cold sprayed WC-17Co coating (a) and WC-17Co+Ni coating with the Ni mass fraction of 20% (b)
Cu-clad diamond/Cu-clad diamond+Cu onto Al substrate
The thick Cu-clad diamond or its mixture with pure Cu powder were successfully deposited onto Al substrate with helium as the driving gas. Fig. 2 provides the morphology of the powders used in this work.
Fig. 2. Morphology and characterization of copper and copper-clad diamond powders used in this study. (a) copper, (b) copper-clad diamond and (c) cross-section of copper-clad diamond
Coatings with different fractions of copper and copper-clad diamond powder mixture were fabricated. For convenience, P represents pure Cu coating, P1 represents Cu-clad diamond+Cu coating (1:8 by weight), P2 represents Cu-clad diamond +Cu coating (1:1 by weight), P3 and P4 represent pure Cu-clad diamond coatings.
Fig. 3a shows the XRD analysis of each coating. There were no diamond graphitization happening due to the low processing temperature for each coating. In addition, the most important finding here is the diamond in the original feedstock almost completely retained in the pure Cu-clad diamond coatings (P3 and P4) which contains more than 40 wt.% diamond.
Such high mass fraction of diamond has never been achieved in previous cold spray works with conventional pre-mixed powder. The mechanically mixed Cu-clad diamond+Cu also exhibited great retainability for diamond; the diamond fraction in the coating was even larger than that in the original feedstock (P1 and P2).
Fig. 3. XRD analysis (a) and element analysis (b) on the coatings
We also investigated the coating microstructure as this is also a very important factor to the final coating performance. Fig. 4 shows the cross-sectional SEM images of the Cu-clad diamond coatings.
It is seen that diamond was seriously fractured in the pure Cu-clad diamond coating. However, considering the very large fraction of diamond in the coating, such fracture can be accepted. In addition, it is also found that additional Cu powders acted as a buffer, effectively preventing the fracture of diamond in the coating.